CASE
Nisbets Catering equipment
From surplus to smarter packaging
Nisbets is one of the largest suppliers of non-food catering items in Europe. The Eindhoven company supplies everything you’d see in a hotel, restaurant or café: from crockery and chef’s knives to refrigerators and items of furniture. Tenfold helped Nisbets improve efficiency by solving its packaging problem.
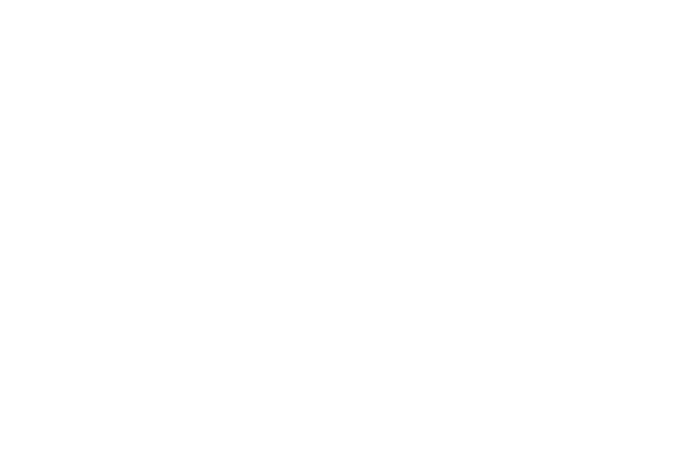
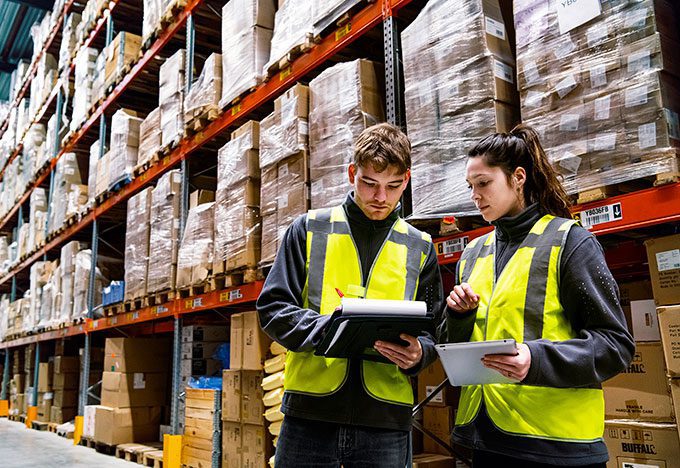
How can we improve continuity without carrying a huge stock of packaging?
Continuity of supply is often a matter of puzzle solving. Naturally, in order to be able to deliver on time and according to need, your stock of packaging material must be in place. The moment Nisbets knocked on our door, the sticking point was clear. The catering articles supplier was getting supplies of cardboard from their parent company in England. But the minimum order quantity was fixed at a higher level than Nisbets strictly needed. The result: an ongoing cardboard surplus on the Nisbets site.
We saw that it could all be done smarter. But rather than just solving this issue in isolation, we looked at the whole Nisbets picture. That took real partnership. Together with our client, we started investigating how we could tackle both this problem and other areas for improvement that we encountered.
A thorough analysis of the packaging process
We meticulously mapped out the entire packaging process. From the moment products arrived, to handling, to when they left the building. How did the lines run? Where were the bottlenecks? What could be faster? In short: what efficiency gains could we make? After all, packaging is about more than simply wrapping something around something. It is an entire process that requires strict organisation. By combining insights from our different divisions, we found the optimal packaging solution.
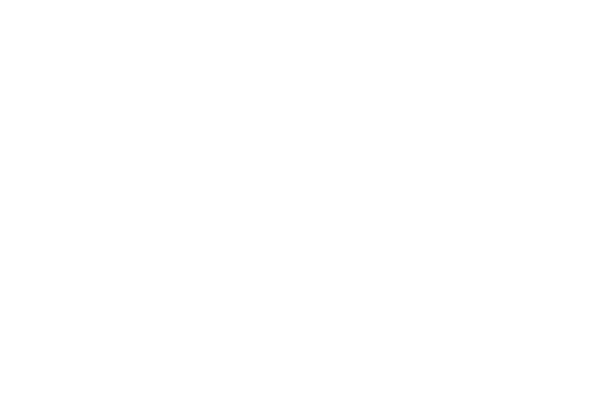
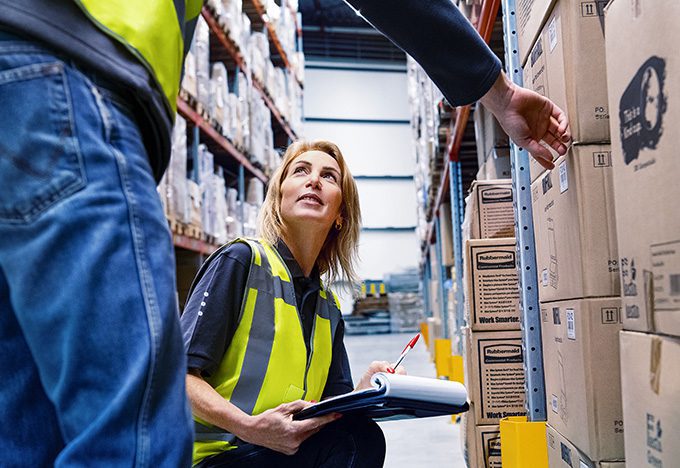
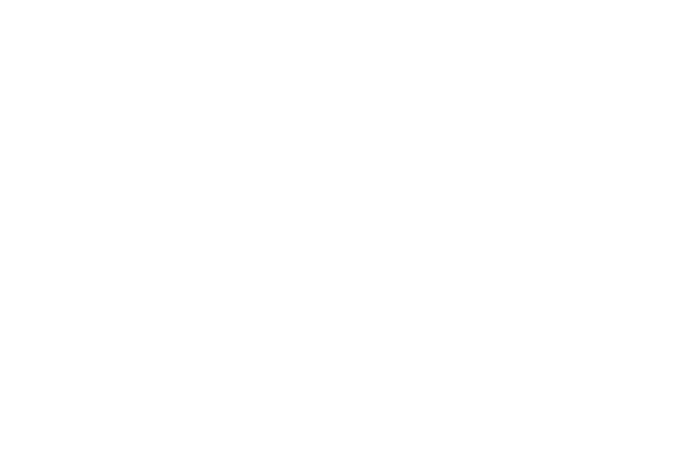
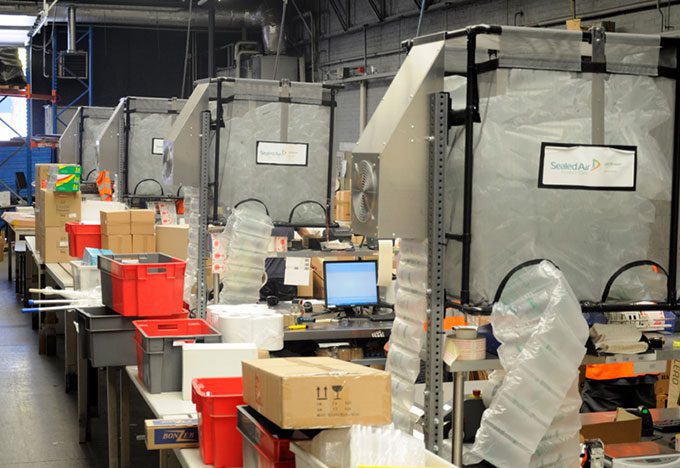
Smaller stock, shorter distances, less consumption
From our analysis of the packaging process, we noticed that Nisbets employees were having to cover relatively large distances to do their job. We streamlined this and improved organization by integrating the filling material more intelligently into the process. We also opted for a different material altogether. The new air cushions we specified are almost CO2 neutral and fewer are needed compared to the old filling material.
Returning to Nisbets’ original question: we have set up a tightly organized paging system. Now order sizes have been reduced from approximately 30 pallets per type of packaging material to between two and six pieces at a time. So consignments are never too big. If Nisbets orders from us today, we’ll deliver it tomorrow. That saves a lot of space! Overall this has been a process in which we worked closely with each other. We searched for solutions together in an open way. And found them.